0引言
联络通道是连接主盾构隧道的重要结构,具有应急救援和防灾疏散的功能,与主隧道形成交叉结构,在开挖过程中受力复杂、施工风险高,因此联络通道结构的安全性备受关注。机械法凭借高效率、高安全性的优势,逐渐成为修建盾构隧道联络通道和废水泵房等工程的重要施工方法。
目前,机械法施工联络通道的反力模式主要为背推式,掘进推力通过传力构件作用于后方管片。研究者对背推式机械法施工过程中联络通道结构的力学行为展开研究,已取得大量研究成果。管片接缝、管片开洞、管片螺栓等细部构件的受力特征对工程安全性具有重要影响,是目前的研究热点。柳献等考虑环纵向接缝刚度非线性,采用荷载-结构计算模型,研究了拆除管片和拆除内部支撑后结构的整体力学性能,阐明了衬砌管片、管片接缝和内支撑体系的协同受力特征。朱瑶宏等通过7环足尺试验,模拟机械法联络通道破洞过程,分析了各衬砌环结构的收敛变形,纵缝及环缝张开位移、错台位移及结构内力等指标,明确了切削过程中主隧道衬砌结构的力学响应。赵泽昌等基于宁波市轨道交通5号线联络通道工程,采用数值模拟方法研究了施工过程 对主隧道管片、螺栓和内支撑体系的影响。
为节省作业空间,提高结构安全性,研究人员提出了反力模式为反拉式的施工工法。与背推式不同,反拉式是将掘进推力通过传力构件反拉于特殊管片。研究者虽然对背推式反力模式下主隧道管片、管片接缝及螺栓等细部构件的受力特征进行了研究,并已取得丰富的成果; 但对反拉式反力模式下主隧道管片、管片接缝及螺栓受力特性的研究较少。
此外,为简化计算,研究者常采用弹簧接触模拟螺栓作用,无法模拟螺栓真实的受力状态;采用摩擦接触模拟管片接缝效应,模型存在大量接触,存在计算难收敛的问题。初步研究结果表明,反拉式反力模式在控制管片变形等方面表现更优。然而,采用反拉式顶管法施工联络通道时,施工过程对主隧道管片力学行为的影响机制不明确,需进一步研究。
在此背景下,本文依托北京地铁某盾构区间联络通道,阐述反拉式顶管法的工艺原理,建立该工程的精 细化数值模型,研究采用反拉式顶管法施工联络通道过程中主隧道管片、管片接缝及螺栓力学行为的演化机制。
1联络通道反拉式顶管法
1.1工程概况
依托工程为北京地铁某盾构区间,其地质条件及联络通道示意见图1。主要地层为粉细砂、黏质粉土、砂质粉土和粉质黏土。场地地表以下60 m深度内一般赋存3层地下水,分别是潜水〈2〉、层间水〈3〉及承 压水〈5〉;联络通道位于承压水〈4〉和承压水〈5〉内。联络通道覆土24.31 m,隧道围岩处于⑥粉质黏土层 和⑦2 粉细砂层。主隧道外径6.4 m、内径5.8 m、环宽1.2 m,每环含6块管片,隧道顶部距地面22.91 m。联络通道始发和接收处分别采用2环钢管片,钢管片采用Q235B钢,其余采用平板式单层预制钢筋混凝土管片衬砌,混凝土强度等级为C50高强混凝土。管片外径均为 3.6 m,内径均为3.1 m,厚度均为0.25m。钢筋混凝土管片环宽为0.55 m,钢管片环宽为0.5 m。
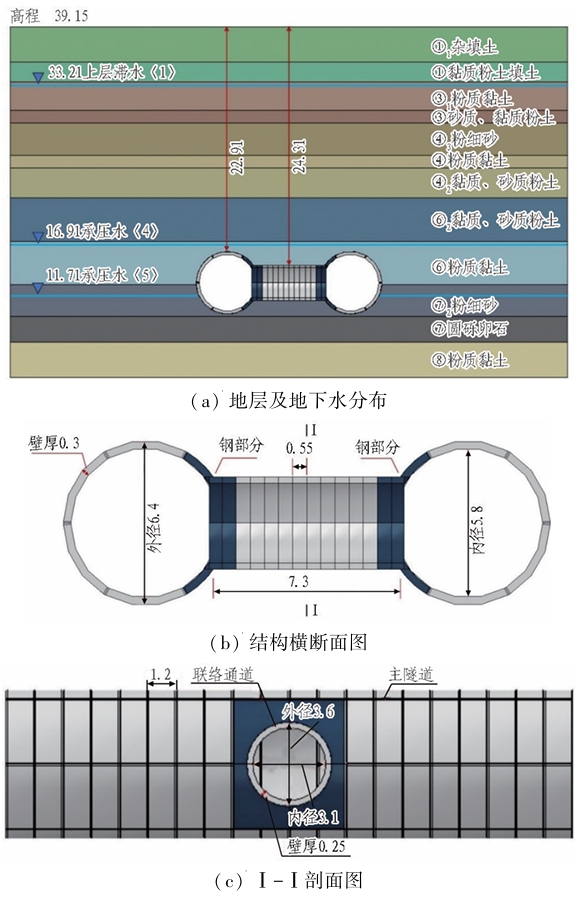
图1地质条件及联络通道示意图(单位: m)
1.2反拉式顶管法工艺原理
本工程采用中国首台反拉式联络通道掘进机进行施工。主隧道联络通道交叉处设有特殊管片,包含外部钢管片及洞门处可切削的混凝土管片。施工流程见图2(a),主要包括: 1)对洞门中心进行复测, 然后进行洞门处及其前后5环管片注浆、特殊管片 中钢管片的接缝焊接等洞门微加固工作; 2)套筒连接就位,并将4套常规顶管机支撑千斤顶反向与洞门周围钢管片连接就位; 3)在套筒的保护下依靠4 套千斤顶的拉力,反向加载推进,通过掘进机切削管片混凝土完成破洞; 4)开挖联络通道土体及拼装衬 砌,进入正常掘进阶段; 5)安装接收套筒,在套筒的保护下破除对面洞门并拼装衬砌; 6)对联络通道管节进行壁后填充注浆,对联络通道钢管片与主隧道管片间隙进行注浆封堵,拆除套筒,采用钢板将联络通道钢管片与主隧道管片焊接,设备出洞并施作洞门混凝土结构。
本工程主隧道管片环宽为1.2m,每环含6块管片。其中,在联络通道洞门开口附近连续4环进行特殊化设计,将每环的2块普通钢筋混凝土管片(4环共8块)整体替换为钢-混凝土复合特殊管片,如图2(b)所示。特殊管片由洞门处可切削混凝土管片及外部钢管片组成。联络通道施工过程中实时监测 特殊管片与相邻管片间错台位移,测点位置如图3 所示。
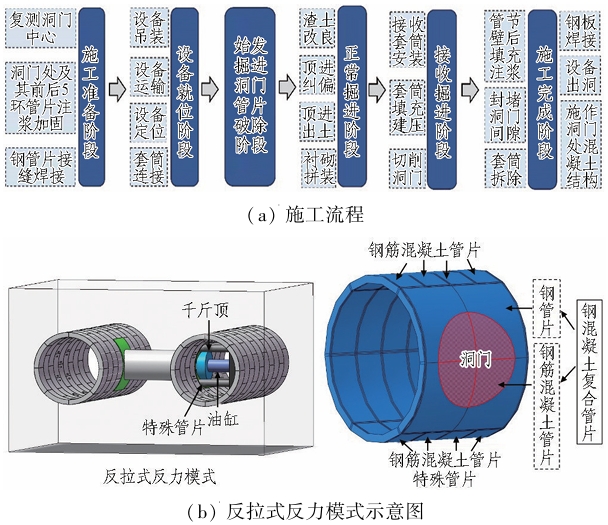
图2反拉式顶管法工艺原理
2数值模型的建立与验证
2.1数值模型
依托工程建立有限元数值模型,如图4所示。左右隧道中心相距12.58 m,两边缘相距18.98 m。考虑边界效应,联络通道掘进方向土体长度设为56.94 m。主隧道掘进方向左右各取20环钢筋混凝土管片,即为24 m;每块管片纵向设3只M28螺栓, 环向设2只M28螺栓,采用Q235B钢。管片破除、联络通道土体开挖和衬砌布设均采用生死单元方法模拟,联络通道单次开挖长度为0.5m,开挖后加设衬砌管片。
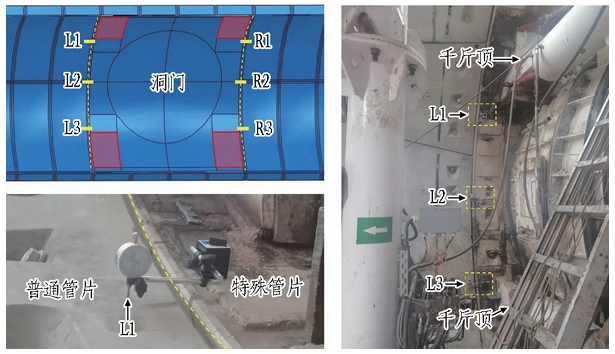
图3管片错台位移测点布置
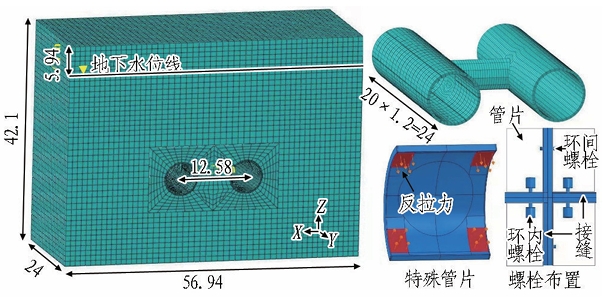
图4 数值模型(单位: m)
联络通道采用反拉式反力模式掘进,模型中将反拉力和扭矩均匀作用于特殊管片内表面,反拉力的方向指向隧道中心。根据现场实测数据,破除左侧管片时,反拉力设为2 000kN,扭矩设为170 kN·m;管片破除后,反拉力设为4000 kN,扭矩设为380 kN·m。采用三维实体螺栓杆嵌入管片来模拟螺栓。为保证计算的收敛性,管片间不设置接触; 在管片间设置接缝区域,管片间通过接缝区域的实体单元连接,接缝区域宽度设为管片宽度的1%,弹性模量设为管片的0.3‰,采用接缝区域实体单元对管片错动的约束作用模拟管片间实际的摩擦接触作用。模型中土体采用摩尔-库仑弹塑性本构模型,其他材料采用线弹性本构模型,均采用C3D8R单元。
根据工程土层特性设定土体渗透系数,以体现地下水的影响。在有限元软件的边界条件模块,将地下水位线处孔压设定为0。模型所采用材料的物理力学 参数见表1,其中,土体参数由工程勘察报告得到,C50混凝土材料参数根据JTG D62—2004《公路钢筋混凝土及预应力混凝土桥涵设计规范》及GB 50009— 2012《建筑结构荷载规范》取值,Q235B钢材料参数根据GB/T 700—2006《碳素结构钢》取值。
表1模型所采用材料的物理力学参数
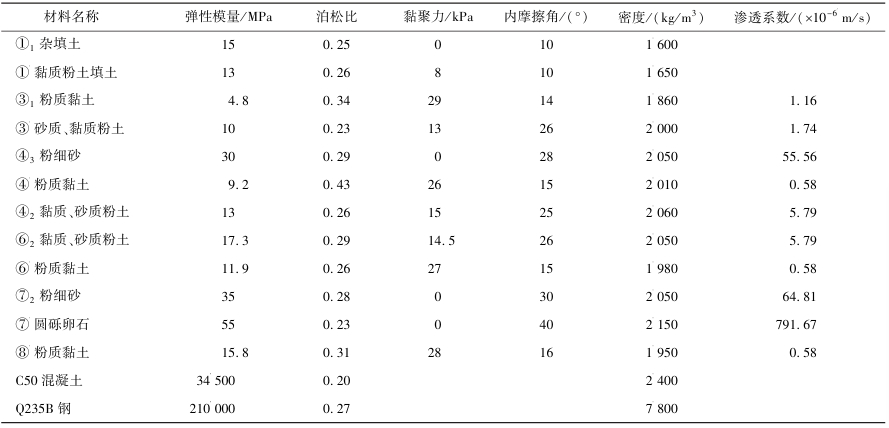
2.2模型验证
特殊管片洞口破除及联络通道开挖过程中,主隧道管片应力重分布,管片环间发生错台位移,引起螺栓及管片结构破坏。特殊管片与左、右侧相邻管片间错台位移实测数据与数值模拟结果如图5所示。
由图5可以看出: 开口左右对称测点的错台位移 相近,开口底部的错台位移最大,开口顶部的错台位移次之,开口中部的错台位移较小。这说明联络通道的施工对管片顶部与底部的错台位移影响较大,管片顶 部和底部为结构的危险部位;而管片中部不会发生较大错动,较安全。左侧主隧道管片破除时,底部L3/R3与顶部L1/R1测点的错台位移急剧增大。其中,L3测点处错台位移最大,为0.63 mm,这说明左侧管片破除时为管片发生较大错动的危险时期,需及时监测错台 位移数据,并采取应对措施。左侧管片破除后,随着联络通道的掘进,错台位移增速虽然变缓,但仍在增加。其中, L1、L2、L3测点处错台位移最大值分别为0.88、0.39、1.17 mm。通过对比6个测点的数值模拟与实测结果可知,数值模型计算得到的错台位移值与实测值吻合较好,误差在20%以内,验证了所建数值模型的准确性。
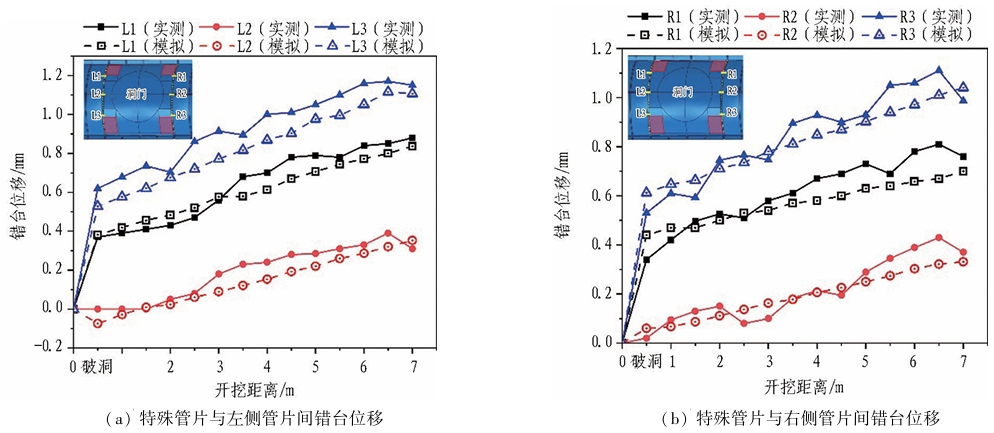
图5 实测与数值模拟的管片错台位移
3特殊管片与螺栓力学特性分析
3.1特殊管片应力演化规律
联络通道顶管法施工首先进行左侧主隧道管片破除,然后依次开挖联络通道土体及布设管片,最后破除右侧主隧道管片。选取6个代表性施工阶段,分析联 络通道施工过程中特殊管片应力演化规律,如图6所示。由图可知: 左侧主隧道管片在破除前处于地应力平衡状态,特殊管片所受最大拉应力为8.8 MPa,最大 压应力为9.8 MPa。左侧主隧道管片破除后,特殊管片处应力重分布,在洞口顶部及腰部出现应力集中。其中,最大拉应力出现在洞口顶部,为15.0 MPa; 最大压应力出现在洞口腰部,为26.2 MPa。随着联络通道的掘进,管片最大应力逐渐增大,当联络通道掘进1m时,压应力达到峰值,为27.0 MPa; 在破除右侧主隧道管片前,拉应力达到峰值,为18.6 MPa。特殊管片采用Q235钢,满足强度要求。
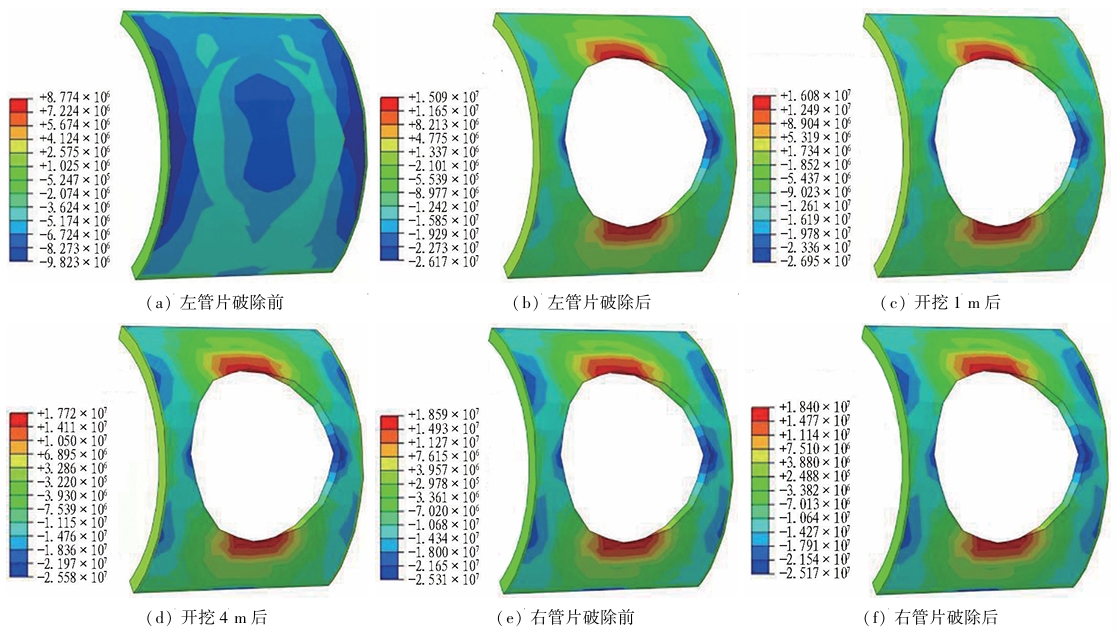
图6开挖过程中特殊管片最大主应力云图
3.2特殊管片横向扩张位移演变规律
左侧主隧道管片破除后,特殊管片产生应力集中, 洞口出现横向与竖向位移。施工过程中特殊管片内凹 侧横向扩张位移(A、B点相对位移)如图7所示。由图可知: 左侧管片破除后,特殊管片发生横向扩张,在洞口左右边缘处横向扩张较大。这是因为: 开洞后,特殊管片原始应力平衡状态被破坏,管片在周围土体产生的荷载及邻近管片的约束作用下发生应力重分布,管片所受竖向荷载较大,管片被压扁,并发生横向扩张位移。左侧管片破除对横向扩张位移的影响显著,左侧管片破除后,横向扩展位移为2.035 mm; 随着联络通道的进一步掘进,横向扩张位移变化缓慢,呈先增大后减小趋势,掘进2.5 m时达到峰值,为2.13 mm,较管片破除时增加了4.7%。当右侧管片破除并布设管片后,横向扩张位移为2.07mm。随着联络通道土体的挖除,特殊管片周围土体应力状态受到影响,发生横向位移的改变。
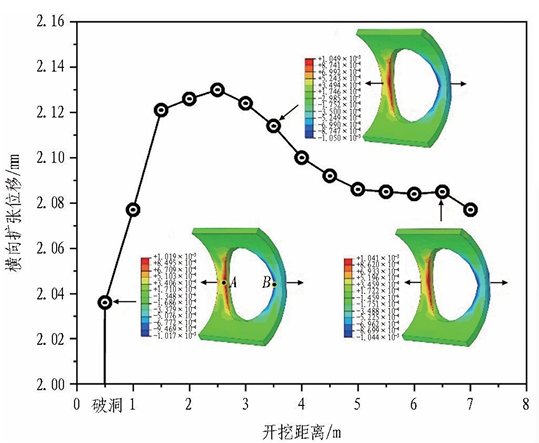
图7施工过程中特殊管片内凹侧横向扩张位移
3. 3特殊管片竖向收敛位移演变规律
施工过程中特殊管片内凹侧竖向收敛位移(C、D 点相对位移)如图8所示。由图可知:左侧管片破除后,特殊管片发生竖向收敛,在洞口上下边缘处竖向收敛较大。 这是因为:开洞后,特殊管片发生应力重分布,管片顶部与底部在竖向荷载作用下分别出现向下和向上的竖向位移,管片沿竖向收敛,管片环呈横向扁平状。左侧管片破除对竖向收敛位移的影响显著,左侧管片破除后,竖向收敛位移为4.26mm。随着联络通道的进一步掘进,竖向收敛位移缓慢增大,掘进2.5m时,变化趋于稳定。当右侧管片破除并布设管片后,竖向收敛位移为4.56mm,较管片破除时增加了 7%。此外,对比图7、8 发现,开挖过程中特殊管片的竖向收敛位移明显大于横向扩张位移,竖向收敛位移约为横向扩张位移的2倍。
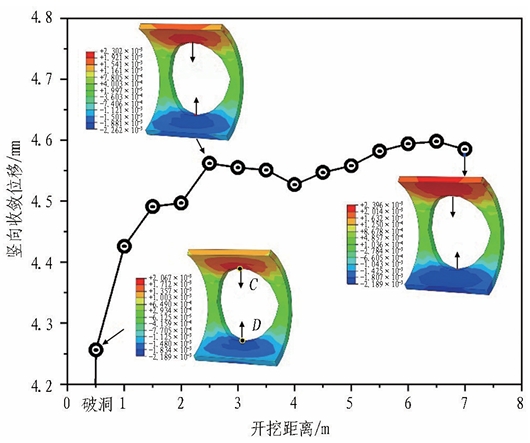
图8 施工过程中特殊管片内凹侧竖向收敛位移
3.4螺栓受力特征
左侧主隧道管片破除及后续联络通道施工过程中,应力不断重分布并平衡,环间管片出现错动位移, 螺栓受力状态发生改变。施工过程中螺栓的受力特性如图9所示。由图9(a)可知,开挖对螺栓的影响范围主要集中在特殊管片与普通混凝土管片连接处的环间 螺栓,对其他区域螺栓受力影响较小。
选取特殊管片与普通混凝土管片左侧连接处的4 个环间螺栓进行分析,螺栓所受最大拉应力如图9(b) 所示。由图可知:上下部环间螺栓(A、D)所受的拉应 力比腰部环间螺栓(B、C)大,左侧管片破除对上下部 环间螺栓的受力状态影响显著。左侧管片破除前,上 下部环间螺栓(A、D)所受拉应力分别为56MPa 和 59MPa;左侧管片破除后,其所受拉应力分别增大至 为174MPa 和166MPa,分别增大2.1倍和1.8 倍。
左侧管片破除使腰部环间螺栓所受拉应力略有减小。 随着联络通道的进一步开挖,上下部和腰部环间螺栓 (A、B、C、D)所受拉应力均缓慢增大,在右侧主隧道管片破除前达到最大值,腰部环间螺栓拉应力最大值为 104MPa,上下部环间螺栓拉应力最大值为213MPa, 接近螺栓屈服强度。这表明:左侧管片破除时,螺栓拉应力增大明显,是关键施工阶段;但随着开挖继续 进行,螺栓拉应力仍在增长,虽然增长较慢,但是仍可能造成螺栓屈服破坏。因此,研究整个开挖过程中特殊管片受力变形特征、螺栓受力状态、管片接缝错动等具有重要意义。
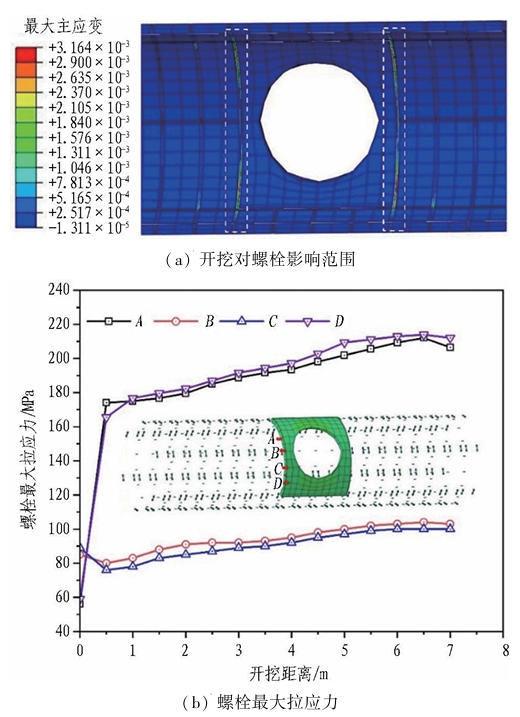
图9 施工过程中螺栓受力特
4反力模式对主隧道管片力学特性影响规律
采用传统背推式顶管法施作联络通道时,推力作用于开口对面管片上;与背推式不同,采用反拉式施作联络通道时,反拉力作用于开口同侧特殊管片上,特殊管 片的受力变形特征发生改变。背推式模型的建模方法 与反拉式模型基本相同,但施工荷载的施加方式不同。背推式模型中将推力和扭矩均匀作用于特殊管片开口 对面内表面,推力的方向由隧道中心指向隧道内壁,推 力和扭矩的数值分别与反拉式的拉力和扭矩相同。
不同反力模式下特殊管片变形如图10所示。由图10(a)可知:采用背推式反力模式时,开口对面管片在背推力作用下发生径向扩张位移,位移最大值为3.54mm;采用反拉式反力模式时,开口侧管片在反拉力作用下发生径向收敛位移,位移最大值为3.02mm。由图10(b)可知:左侧管片破除后,特殊管片开口处发生横向扩张位移(图中最大正负位移绝对值之和), 采用背推式反力模式时,位移最大值为1.8mm;采用反 拉式反力模式时,位移最大值为2.04mm。由图10(c)可知:左侧管片破除后,特殊管片开口处发生竖向收敛 位移(图中最大正负位移绝对值之和),采用背推式反力 模式时,竖向收敛位移最大值为3.09mm;采用反拉式 反力模式时,竖向收敛位移最大值为4.26mm。由图10(d)可知:左侧管片破除后,环间发生错动,采用背推 式反力模式时,开口对面管片环间错动较大,最大主应变为0.53%;采用反拉式反力模式时,开口同侧,特殊管 片与普通管片接缝处错动较大,最大主应变为0.26%。
不同反力模式下特殊管片应力如图11所示。由图11(a)可知:左侧管片破除后,开口顶部和底部承 受拉应力,开口腰部承受压应力。采用背推式反力模式时,顶部和底部最大拉应力为18.4MPa,开口腰部最大压应力为27.9MPa;采用反拉式反力模式时,特 殊管片所受应力略有降低,顶部和底部最大拉应力为 15. 1MPa,开口腰部最大压应力为26.2MPa。此外,采用背推式反力模式时,背推力使开口对面管片产生 较大的拉应力(见图11(b)),易引起普通钢筋混凝土 管片的开裂。
综上分析可知,采用背推式反力模式对控制特殊 管片开口处的横、竖向位移更有利;采用反拉式反力 模式对控制开口对面管片受力变形和接缝处错动位移更有利。
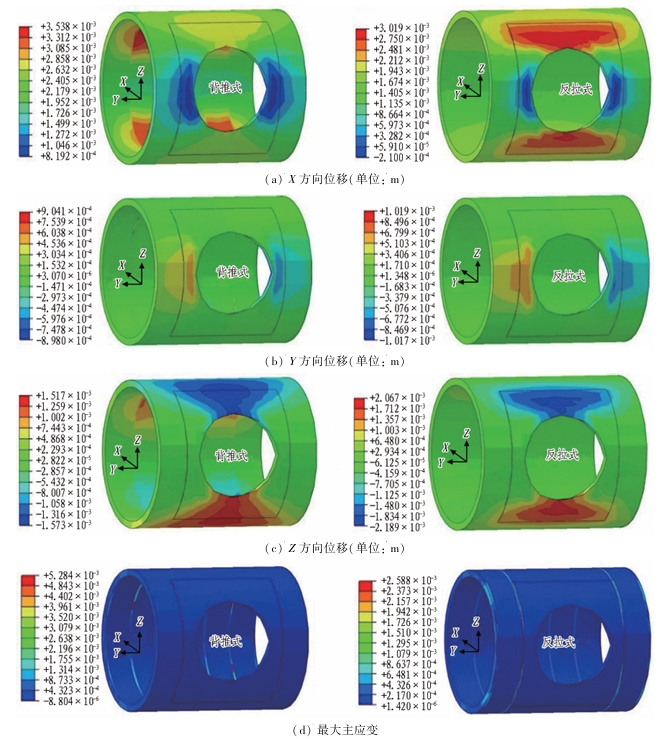
图10不同反力模式下的特殊管片变形
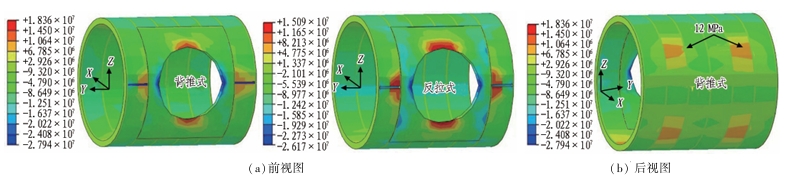
图11 不同反力模式下的特殊管片应力
5结论与讨论
本文依托工程实例论述了地铁盾构隧道内采用反 拉式顶管法施工联络通道的工艺原理,建立了三维有限元模型。通过管片变形的现场监测验证了数值模型的计算结果,继而研究了主隧道管片、管片接缝及螺栓力学行为的演化机制,得到结论如下:
1) 本文所建立的数值模型能较好地反映螺栓和管片接缝的实际受力状态,计算得到的错台位移值与实测值误差在20%以内。
2) 联络通道开挖初始,洞口管片破除对主隧道力学性能影响显著。管片破除后,联络通道的继续开挖使管片错台位移、特殊管片应力及变形、螺栓受力逐渐增大,虽然增长缓慢,但仍可能造成危险。开挖过程中,管片间最大错台位移为1.17 mm,发生在特殊管片与普通管片接缝的底部位置。特殊管片最大拉应力为 18.6 MPa,发生在开口的顶部和底部;最大压应力为27.0 MPa,出现在开口的腰部;最大横向扩张位移和竖向收敛位移分别为2.13 mm和4.56 mm。
3)背推式反力模式更利于控制特殊管片开口处 的横、竖向位移,反拉式反力模式更利于控制开口对面管片受力变形和接缝处错动位移。本文对反拉式顶管法施工联络通道过程中主隧道力学性能进行了初步研究,今后仍需进一步研究特殊管片型式及开口尺寸、施工荷载及加固条件的影响,以 及反拉式顶管法施工联络通道过程中主隧道管片的力学响应机制。