2022年10月31日,国内整体规模最大的内河沉管隧道——襄阳市襄江大道鱼梁洲隧道建成通车。襄阳市襄江大道鱼梁洲隧道是连接襄阳市东津新区与樊城老城区的一条快速通道,起于大庆东路东侧,途径城市“绿心”鱼梁洲,止于纵四路西侧,全长5.4公里,采用双向六车道城市快速路标准建设,主线设计时速60公里。鱼梁洲过江隧道通车使东津到樊城的行车时间从45分钟缩短至10分钟以内,加快了东津、樊城新老城区的联通联动,实现了襄阳内环线、绕城高速与樊城、鱼梁洲、东津新区的快速连接,使外环高速与内环快速路得以有效串联,成为引导城市向东拓展、带动人口聚集和功能转移的重要交通轴、发展轴和景观轴,为襄阳市打造“一心四城”空间布局结构提供“加速度”,促进区域经济发展,有效提升襄阳的区域影响力,助力襄阳打造省域副中心城市。项目严格遵循生态保护原则,总体采用隧道结构,其中明挖暗埋隧道长4.03公里,明挖敞开隧道长0.36公里,两次下穿汉江的沉管隧道长1.01公里,是千里汉江第一条公路隧道,也是华中地区首条内河沉管隧道。
襄阳鱼梁洲隧道概况
1工程规模及技术标准
襄阳鱼梁洲隧道是连接襄阳市樊城、鱼梁洲、东津3个核心城区的中轴线道路工程。隧道全长5 400 m, 在西汊和东汊各设置长351、660 m沉管隧道下穿汉 江,共10个管节,其他区段采用明挖隧道;沉管采用长距离双轴线干坞预制方式。隧道采用设计车速为 60 km/h双向6车道城市快速路标准,建筑限界净宽 为12.25 m,主体结构设计使用年限为100年。
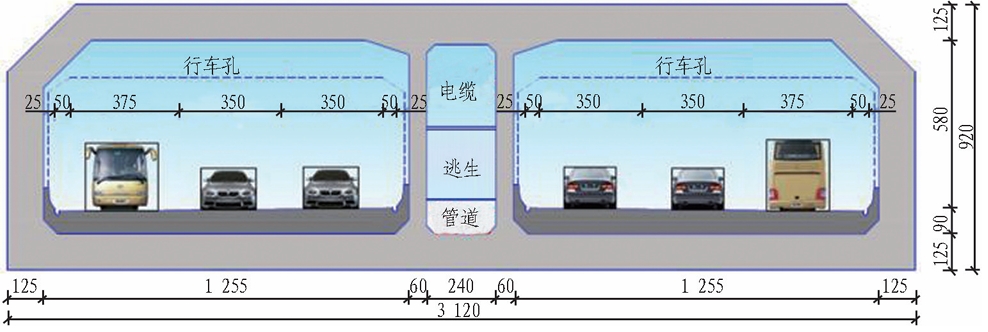
鱼梁洲隧道沉管横断面布置(单位: cm)

鱼梁洲隧道平面图
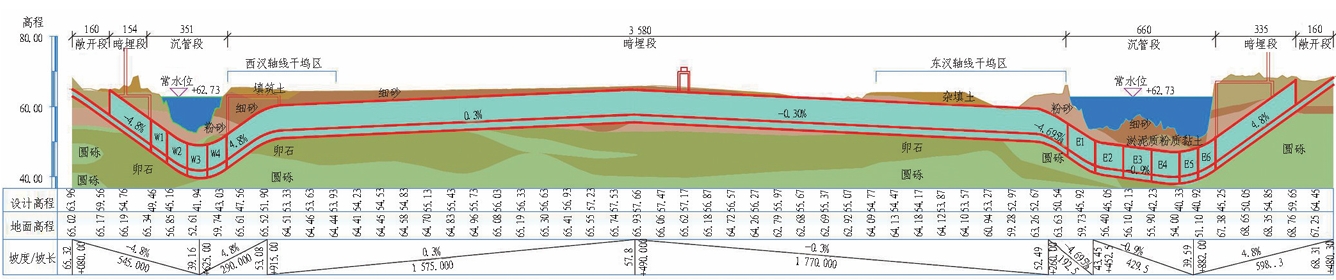
鱼梁洲隧道纵断面图(单位: m)
2建设条件特点
鱼梁洲隧道场区地层上部为填土和薄层淤泥,中 部为粉细砂(渗透系数16 m/d),下部为深厚卵石、圆砾(渗透系数25~102 m/d);稳定黏土不透水地层埋 置深度达55~100 m; 隧道基底为基本位于砂层或卵 石圆砾层。项目区汉江水流速度为0.57~3 m/s,水位 差为2.2 m。受中游区水文特点及多江汇流影响,项 目区河床总体呈汛期大冲刷、汛后大回淤状态。东西 汊河床断面最大预测冲深分别达7.7 m和5.1 m,最大预测淤深分别达3.7 m和2.6 m,最不利位置处冲淤差达10 m。隧址区东西汊水面宽度分别仅约600 m和300 m,且存在现状Ⅳ级航道,大型船机作业条件受 限。沉管隧道建设需在4处破除现状汉江大堤,破堤 总宽度约300 m,对汛期岸堤防洪存在较大影响。
强冲刷条件下沉管埋深控制及防冲保护技术
根据国内相关规范要求,沉管及其硬壳保护层宜 设置于预测最大冲刷线以下。鉴于内河中游区河床冲 刷深度通常较大,按最大冲刷线进行沉管埋深控制会 导致隧道覆土大、接地距离远、服务功能弱化。因此,科学量化评价高流速条件下的沉管冲刷安全并合理确 定沉管埋深是内河中游区沉管建设的关键。
1高流速条件下沉管冲刷安全评价标准
综合考虑锁定回填阶段沉管结构横向稳定性、管 顶回填材料抗冲稳定性及构造合理性、河道行洪过流 能力保障性、河流壅水水位等评价因素,采用数值模拟 和理论分析手段进行冲刷安全评价标准研究。
沉管周边水流场分析:通过数值模拟研究沉管结构凸出河床不同高度工况的周边流场变化分析可知,随着沉管结构凸出河床高度加大,隧道顶部最大流速呈线性增大趋势。建立工程河段隧道凸出河床高度 占比H与河流流速增加率V之间的关系: V=2.197 5H+0.978。可通过该公式预测隧道凸出河 床不同高度工况下的流速值。
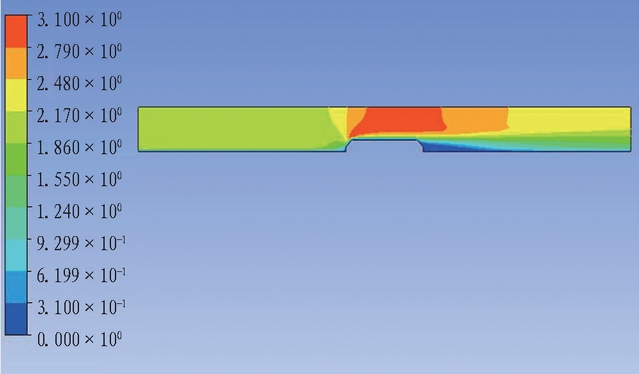
沉管隧道凸出河床对周边流场流速分布影响(单位: m/s)
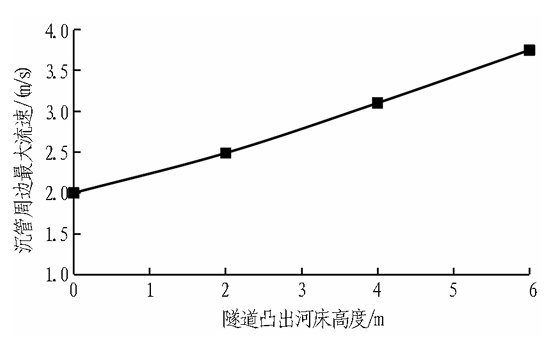
沉管隧道凸出河床高度与周边最大流速关系
沉管冲刷安全评价指标及标准:结合模拟计算分析得出的规律特点、结构安全需求和相关规范要求,沉管抗冲刷安全评价需考虑锁定回填及管顶回填2个阶段共5项评价指标。在进行沉管冲刷安全评价时,可结合工程河道、水文、隧道结构等情况,对评价指标采用表中方法进行逐一评价,同时满足所有指标评价标准的隧道埋深即是满足沉管冲刷安全评价的合理经济的隧道埋深。
沉管冲刷安全评价指标及标准表
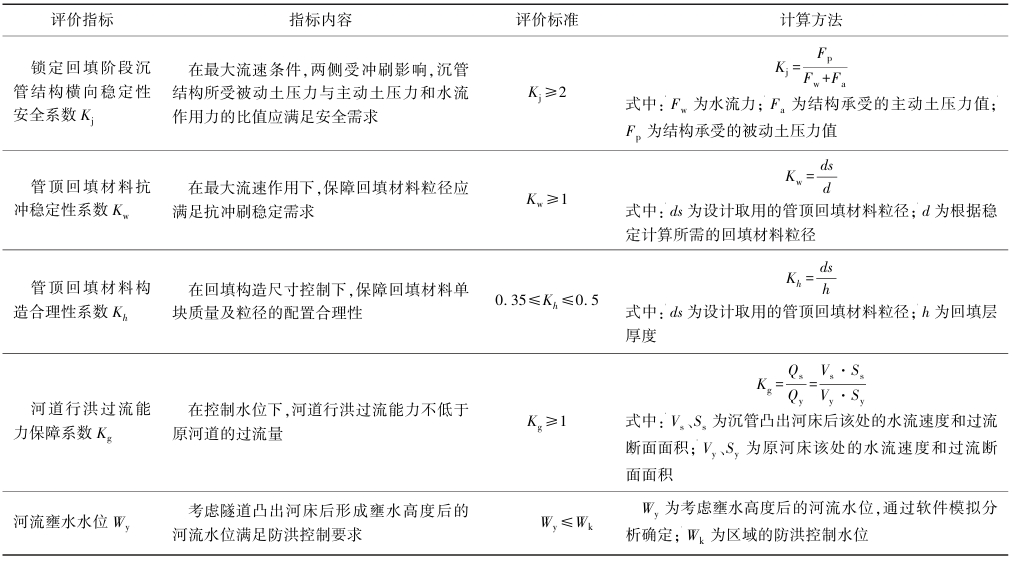
2防冲保护结构对隧道埋深的影响及合理埋深确定
当沉管结构突出冲刷线,面临较大防冲稳定风险时,可通过在管顶设置雷诺护垫、格宾网、块石、软体排 等典型防冲刷措施,提升抗冲能力,保障河道过洪能力。结合模拟计算分析,采用前述冲刷安全评价方法, 研究采用不同等级的防冲保护措施工况下隧道允许凸出河床的高度。鱼梁洲隧道在上游150 m、下游100 m范围内,采 用顶面铺设软体排、1 m厚块石压载、周边格宾石笼网 压重的方式进行防冲保护。隧道埋深结合冲刷安全评价方法确定,较不设防冲保护 措施抬升约2 m,有效降低了隧道规模和工程造价,增 强了交通服务功能。根据运营期间沉管结构水平位移和防冲保护层监测,结构处于稳定状态。
不同等级防冲保护措施对应隧道允许凸出河床高度
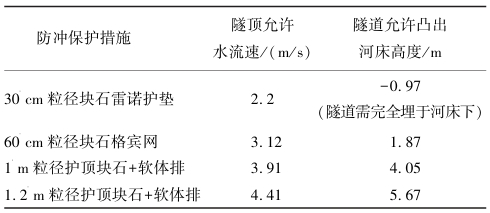
3近岸深埋段隧道防冲减载复合功能回填结构
近岸深埋隧道上方回填需考虑结构防冲和减载双重功能。减载方式主要有设置架空层减载、空箱减载、轻质材料回填等。综合考虑工艺工序、工期、造价等因素,依托工程采用泡沫轻质混凝土预制块作为岸堤减 载兼防冲回填结构。 泡沫轻质混凝土密度、强度的耐久性是其作为减载材料需解决的核心问题。通过物模试验建立泡沫轻质混凝土湿密度与耐久性关键指标的关系;随着泡沫轻质土湿密度的增加,泡沫轻质土的质量损失率和强 度损失率均逐渐降低;当泡沫轻质土湿密度在FA6级 (约1300 kg/m3)以上时,其质量损失率和强度损失率 可分别控制在0.28%和15%以下,满足本项目100年使用年限要求本项目最终采用湿密度1 300~1 400 kg/m3,28 d抗压强度不小于2.6 MPa的 泡沫轻质预制块体进行减载,单块体尺寸1.8 m× 1.8 m×0.9 m,采用船机吊放安装。
深厚强透水地层无内撑干坞深基坑设计施工关键技术
依托工程采用1 200 m长距离双轴线干坞进行沉管预制,干坞处于汉江冲刷堆积形成的江心鱼梁洲,洲 上强透水砂卵石地层深达55~100 m;干坞最深处达 24 m,内部需提供无内撑开敞作业条件,坞口结构需提 供汛期岸堤防洪、管节出运、二次止水封闭等功能;干 坞基坑使用周期长达18个月。合理确定坞内基坑支 护体系、坞口岸堤保护结构和超大基坑降止水措施,是 依托工程沉管干坞建设的关键。
1强透水砂卵石地层预应力锚索地下连续墙技术
为满足轴线干坞开敞作业需求,依托工程西汊干坞 基坑采用了锚索地下连续墙无内撑支护方案。针对基 坑处于粉细砂及卵石复合地层的特点,开展现场锚索拉 拔试验,建立适用于锚固段穿越双地层的拉力型预应力 锚索弹簧-粘片力学模型,给出锚索锚固段 剪应力状态处于不同阶段时的锚固段剪应力分布及拉拔力-始端位移理论关系式。通过将弹簧-粘片力学模 型与现场拉拔试验相结合,对预应力锚索极限黏结强度进行了半解析预测,获取砂层与卵石层黏结强度取值分 别为30 kPa和200 kPa。k为弹簧刚度系数; C1为上部地层中粘片的极限黏结强度; C2为下部地层粘片的极限黏结强度。
结合上述分析,依托工程设计采用长度为15~20 m 的3层锚索,层间距2.5 m,锚固段长度为10~14 m。锚索施工采用“跳孔钻进 法”工艺,实现锚索钻孔和压浆互不干扰,避免砂卵石地层塌孔、难成孔问题。 通过一次常压注浆加二次高压劈裂注浆,实现锚固体饱满;通过端头堵水型锚头和 细石混凝土永久包封,实现施工期堵水。根据现场监测结果,预应力锚索段基坑地下连续 墙最大水平位移为9mm,围护结构受力变形均在安全控制范围内。
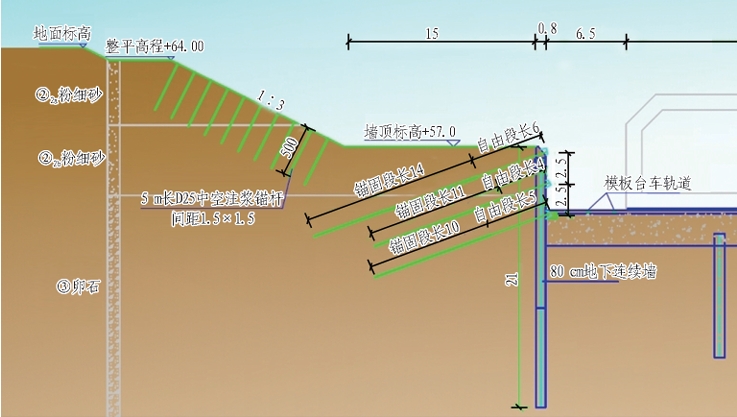
西汊干坞基坑锚索布置图
2干坞口临江超深大型格构式地下连续墙技术
结合坞口结构功能需求和坞外24m基槽开挖深度,东西汊干坞口均采用大型格构式地下连续墙支挡方式。为合理确定格型地下连续墙结构构造,建立格型 地下连续墙数值模拟分析图,开展格型地下连续墙墙体厚度、前后墙间距、隔墙间距、前墙深度、隔 墙深度及后墙深度等构件参数的敏感性分析,获取对 结构变形受力的主要影响因素。
根据现场监测结果,基坑使用期内干坞口格型墙 最大墙顶位移25mm、最大深层水平位移40mm,围护 结构受力变形均在安全范围内,止水效果良好。
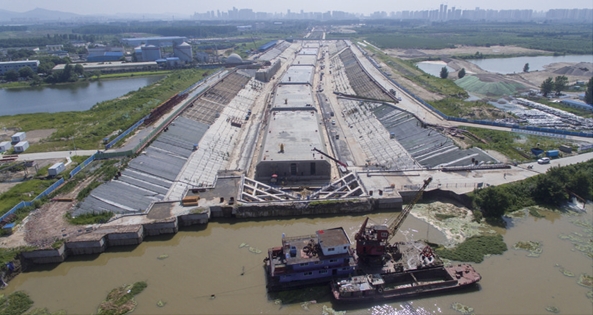
东汊干坞口格型地下连续墙施工现场
3临江深厚强透水地层干坞基坑降止水技术
针对依托工程干坞基坑强透水地层深厚、临江地下水补给迅速、基坑使用周期长等特点,为合理确定干 坞基坑止降水方案,对东汊和西汊干坞不同地层区域 开展井群降水试验。 结合降水试验数据,建立地下水 三维渗流数值模型进行渗透系数反演,得到 砂层、卵石层、圆砾层渗透系数分别为 16、102、 25m/d。 东汊干坞区隔水地层深约60m,基坑采用塑性混 凝土落底式止水帷幕方案;西汊干坞区坞口段和坞尾 段隔水层深度分别约50m和100m,分别采用塑性混 凝土落底式止水帷幕和悬挂式隔水帷幕加混凝土封底的组合止水方案。
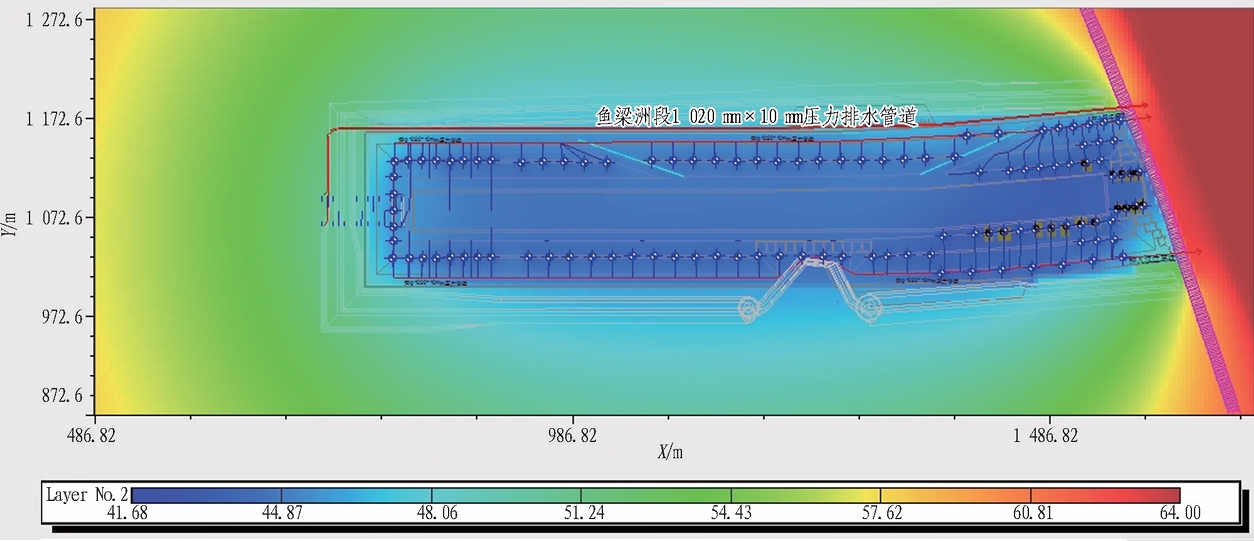
东汊干坞基坑降水数值模拟反演平面云图
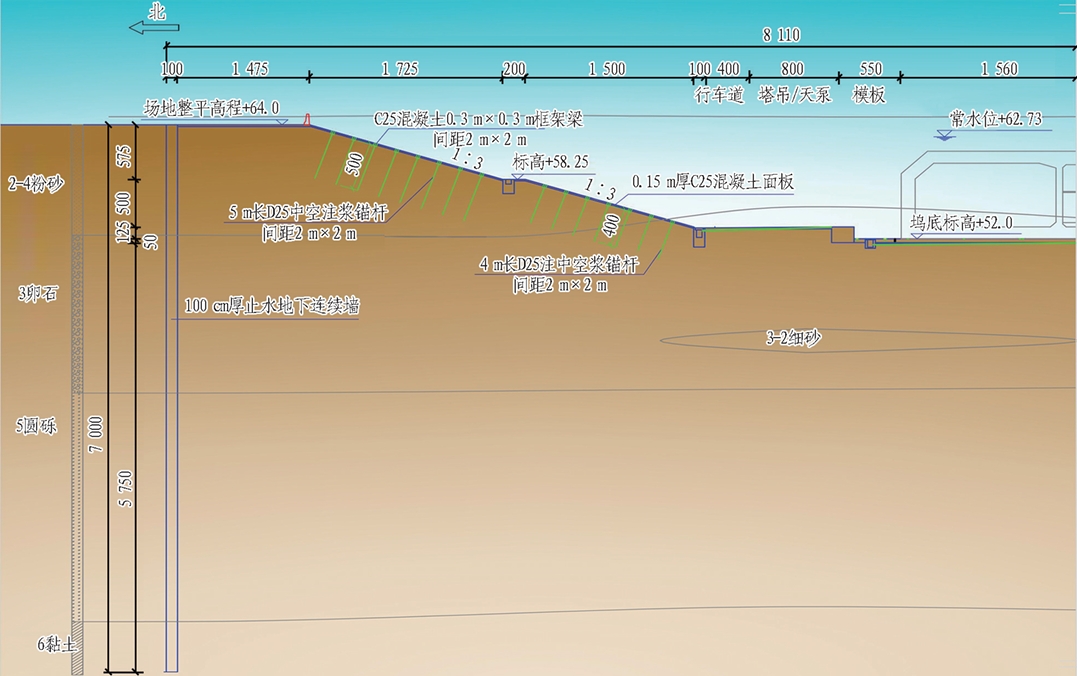
落底式止水帷幕方案图(单位:cm)
为确保施工期降水安全,研发了“水位自动监测+ 电测位计辅助观测”系统,通过信息化监测监控,实现 “分步、按需、受控”降水及降水水位自动实时预警功 能,保证了干坞施工期和运营期的安全。
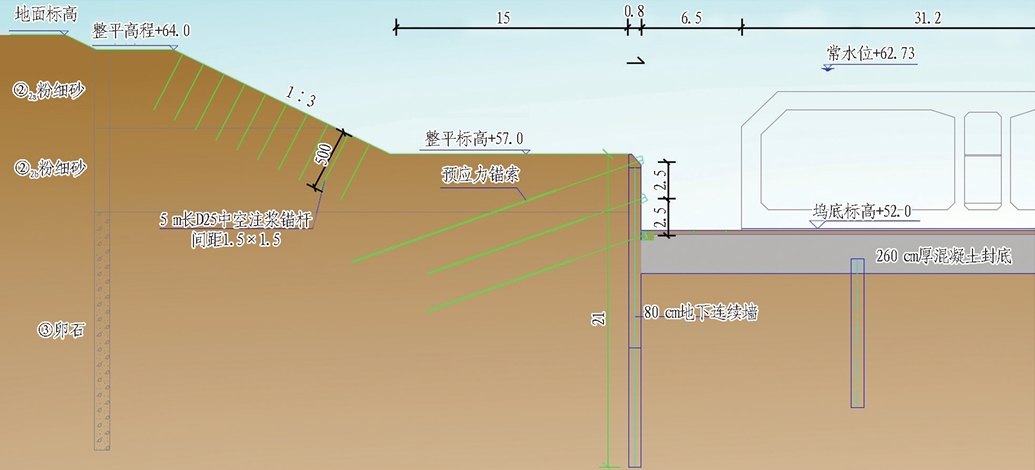
悬挂式隔水帷幕加混凝土封底方案图(单位:m)
摩擦止推型沉管陆域最终接头及对接端二次止水技术
鱼梁洲隧道结合轴线干坞特点采用陆域最终接 头,通常在端部设置止推圬工结构以抵抗抽水后的 GINA 止水带回弹,而止推措施造价昂贵、水下作业 多、工期冗长。 因此,对最终接头止推进行理论和构造创新,同时匹配合理的岸堤对接端二次止水结构,是依 托工程沉管建设的关键。
1沉管基床摩擦因数物理模型试验
提出取消依托工程沉管陆域最终接头止推圬工结构,利用管节周边与回填土体摩擦力止推的技术思路。 为获取准确的管周摩擦因数,通过室内试验设备开展4 种荷载工况9组室内试验,并通过现场试验设备开展考 虑淤泥、涂层的4种工况12组现场水下试验, 通过位移稳定增加阶段水平荷载与竖向压力比值,最终 确定卵石层顶无淤泥和全淤泥工况的摩擦因数分别为 0. 43 和0.24。
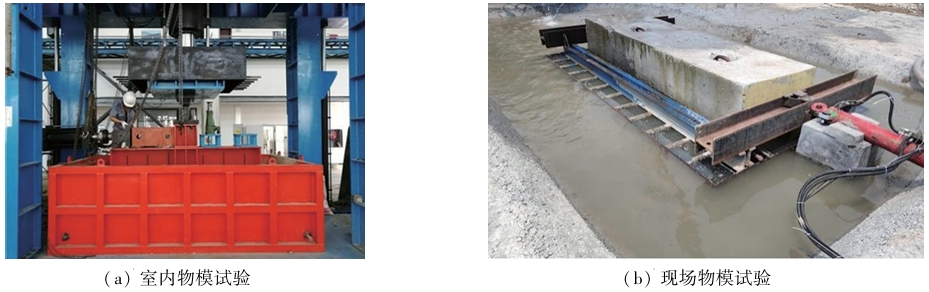
室内和现场物模试验装置
2摩擦止推型沉管陆域最终接头技术
摩擦止推型沉管陆域最终接头的总体工艺机制 如下: 1)干坞内预制5 m长小管节并与最后1节沉 管预先拉合固接为一个整体; 2)管节浮运安装并回 填完成后,通过临时连接措施将临近最终接头的若 干管节通过钢结构连接在一起; 3)在坞口小管节上 方设置二次止水结构封闭坞口并抽排坞内水,利用 管节周边与回填土体摩擦力抵抗各管节间的GINA 止水带回弹力; 4)隧道全部贯通后拆除管节临时连接设施。
3对接端装配式双壁钢围堰二次止水技术
沉管沉放完成后,坞口需实现封闭。结合围护支 挡、防水和安装便捷等功能需求,对接端二次止水采用 分片吊装内灌混凝土双壁钢围堰+内侧主动支撑结构形式。通过不同工况数值模拟分析,钢围堰内填充混 凝土可使变形和面板应力减少90%以上,大幅提升整 体刚度;相较被动支撑,主动支撑可使钢围堰向沉管的 荷载传递减小50%,有利于改善最终接头的止推压 力。钢围堰分片间设置锁扣构造并灌注细石混凝土实 现围堰接缝止水;在钢围堰与两侧地下连续墙及沉管 之间设置预埋钢边止水带并现浇水下混凝土实现侧方 接缝止水;在管节底部传力板上设预留槽并内设2道 类GINA止水带+膜袋混凝土+空隙注浆实现底板接缝 止水。
施工过程中,考虑钢围堰制作偏差、管节制作偏 差及温差影响、GINA止水带材料性能偏差、GINA松 弛影响等4个方面因素,对预留槽定位偏差量进行了分析,其中东汊材料后补充偏差导致累计压缩偏 差约6 cm,最终确定预留槽定位偏差量为±15 cm。 同时,对钢围堰结构进行变形和受力监测,实测最大变形值约5 mm,干坞支撑轴力最大值约1 200 kN,围堰变形和结构受力满足规范和结构 承载能力要求。
沉管接头外侧止水带国产化研制及应用
内河中游区水位季节性变化大,水压周期性变化对 沉管接头水密性要求高;同时,由于沉管接头外侧止水 带在100年设计使用年限内需保持水密性能且无法更 换,其性能指标要求高,目前中国已建的10余座沉管隧 道均采用国外GINA止水带产品。 因此,研制适合内河水文特点的沉管接头外侧止水带,并通过产品国产化打 破国外垄断,是内河沉管隧道建设亟待解决的问题。
1基于物模试验的沉管接头国产化外侧止水带性能指标分析
分析国产止水带的压缩、水密、耐久等性能指标, 验证其适用性,是实现止水带国产化研制的前提。为此,针对国产止水带开展压缩力学性能、水密性能、耐久性能等系列物模试验及测试分析。
在压缩性能试验研究中,通过300t和2500t压 剪试验机,对3种硬度的国产止水带开展正压和偏 压工况的压缩加载试验,获取止水带压缩曲线。 试 验结果显示:随着水压增大,止水带压缩量增大,且 逐渐趋于极限值,该极限值约为初始高度的60%。对国产止水带与国外止水带产品的最 小水密压缩量曲线进行对比,两者基本吻合,在不同水压下所需最小水密压缩量存在0~ 15%的偏差。
2沉管接头国产化外侧止水带设计选型及研制应用
依托工程国产止水带 采用带鼻尖的梯形实心构造,材料采用天然 橡胶。止水带尺寸及硬度选型结合各接头处计算张合 量和止水带性能指标确定,接头张合量计算安全系数在SLS 工况不小于1.75,在ALS下不小于1.25。止水带选型校核需采用最小水密和最大压缩指标双控。
基于依托工程开展沉管接头外侧止水带国产化产 品结构设计、材料配方设计、生产制造等全过程能力建 设,形成了产品性能试验检验技术、生产工艺流程、预 成型工艺、硫化工艺、安装工艺等一整套自主知识产权关键技术。依托工程12处接头全部采用国产止水带,实现了高质量生产制造和现场安装。
整体式管节无后浇段全断面顺浇预制技术
目前中国已建成的内河沉管隧道均采用整体式管节,通常采用分部分层、设后浇带、跳仓等浇筑工艺预 制,而上述工艺存在施工缝及渗漏隐患点多、工艺繁 琐、工期较长等问题。对管节预制工艺进行改进创新, 减少施工缝设置和管节渗漏风险,是内河沉管隧道建 设亟待解决的问题。
1基于数模及物模试验的整体式管节全断面顺浇预制工艺研究
依托工程针对整体式管节提出全断面顺浇预制工 艺,将管节划为多个刚性连接的节段,各节段按顺序依 次全断面一次浇筑成型,其工艺流程可按节段分底板、 侧墙、顶板钢筋绑扎及模板安装、混凝土浇筑及养护5步顺序工厂化流水施工。全断面顺浇预制工艺较常规分部分层后浇带工艺,可减少结构接缝长 度约61%,缩减预制工期约52%。
通过仿真模拟和物模试验,对全断面顺浇预制工 艺的可行性进行验证。试验发现: 控制相 邻节段浇筑间隔时间在7~10 d,可使开裂安全系数控 制在1.4以内,优于后浇带和跳仓法工艺。
2整体式管节全断面顺浇混凝土控裂技术
依托工程管节单节段混凝土浇筑体量达2 460 m3,结构控裂问题突出。通过优化配合比、合理分区浇筑、控制入模温度、控制相邻节段浇筑间隔、接缝处收缩补 偿、智能温控养护等措施进行结构混凝土控裂。通过对水泥品种、碎石比例、胶材用量、矿物掺和 料掺量等进行11组配比试验,以强度、容重、混凝土工 作性能为评价指标,确定最优配合比。
单个节段全断面浇筑按截面分4个区域进行连续浇筑,总浇筑时间控 制在32 h左右。混凝土初凝后到拆模前,采用覆盖土工布洒水养护方式;外模板拆除移位后,采用专用 的自动洒水设备进行喷水养护;内模板移出后,采用 智能超声雾化机养护。结合物模试验,按高温季节浇筑温度≤26 ℃,低 温季节浇筑温度≥5 ℃作为混凝土浇筑温控标准,通 过掺冰拌合控制入模温度,研发出一体化智能温控系 统,可实现混凝土温控智能化监测。针对节段接缝周边区域,提出抗放结合的综合控 裂措施。用钙镁复合膨胀剂改善混凝土补偿收缩性 能,用高性能纤维复合材料提升混凝土抗拉强度、抑制 裂缝。与常规控裂措施对比发现,本文提出的控裂措 施可减少裂缝数量约60%,减少裂缝长度约56%。
内河沉管浮运沉放技术及配套装备研发
内河中游区河床卵砾石资源丰富,汛期回淤强度大,水面通常较为狭窄且需考虑通航,这使得大型船机水面作业的空间和时间受限。依托工程针对上述特 点,对沉管基床材料及其铺设装备、沉管快速装配化舾 装等进行了技术创新。
1沉管全浮式先铺整平卵石基床技术及关键装备
鱼梁洲隧道就地取材将沉管基槽及干坞开挖获取 的大量卵石作为沉管基床材料。通过物理模型试验对 卵石垫层和碎石垫层力学变形特性进行对比研究, 为垫层材料选型和基础设计提供依据。 基于试验获取的卵石基床力学参数,结合垫层及 地基最终沉降量、施工拖曳引起的垫层沉降量、管内空 间需求、GINA止水带对接错位水密需求等因素,提出了基床预抛高值计算方法。未沉放侧预抬量取值为基 础及基础计算最终沉降值+管节拖曳垫层沉降量,对 接侧预抬量取值为垫层计算最终沉降量+管节拖曳垫 层沉降量+管节沉放偏差/2的预抛高。对E4管节沉放后的实测沉降数据与模拟分析结果 进行对比分析,沉管沉放后,前期沉降较大, 沉放完成至加载至5%自重阶段,发生沉降1~2 cm,大于预测值。后期回填阶段发生沉降值为3~4 cm,与预测值基本吻合。
依托工程首次研发应用了适用于内河窄水域的全 浮式高精度基床整平船,该船由浮式驳船+锚泊系统+ 可旋转抛石管组成,可实现作业水深26 m,单次整平 宽度50 m,石料输送600 t/h;研发了基于速度—张力 控制的一键式智能锚泊定位算法,形成了船舶绞车自 动移位与纠偏技术。施工实施验证显示定位精度可 达10 cm内,单垄移船时间小3min,整平精度可 达±3.5 cm。
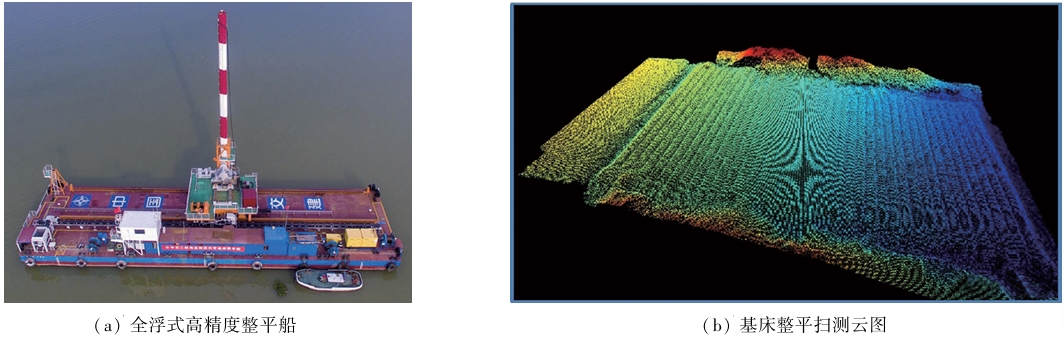
全浮式高精度基床整平船及基床整平效果
2沉管舾装新技术
为提升舾装效率、降低舾装成本,依托工程首次研 发并应用了水压紧密型全装配式沉管钢封门,采用分片装配式楔形结构,通过楔形多孔三元乙丙橡胶条压 缩实现密封防水,无现场焊接工作,可循环利用。配套 研发的具有多向调节功能的安装台车,可实现便捷安装拆卸。
依托工程首次研发并应用了沉管柔性水袋压载水系统,水袋由PVC内囊、编织布、加筋带和涂层4 层组成,工厂内一体化预制;通过双向流量计和压力传感器进行双重水量监测,确保水袋安全;水袋可直接铺于沉管底面,安拆便捷;充水后可适应4.8%大纵坡;可实现水袋压载水系统远程自动控制。该压载水系统较常规系统效率高、成本低。
主要创新成果
依托襄阳鱼梁洲隧道工程,针对内河中游区 冲刷强、强透水地层深厚、防洪要求高等特点,通过工程调研、理论分析、物模试验、数值模拟、现场测试、软件研发等手段,对内河沉管隧道建造关键技术进行创新及应用,形成主要创新成果如下:
1)首次提出了沉管隧道冲刷安全量化评价方法, 给出了沉管结构横向稳定性安全系数等5项评价指标及其评价标准体系,填补了水下隧道领域防冲安全量 化评价方法的空白。
2)首次研发了摩擦止推型最终接头结构,揭示了摩擦止推最终接头结构的工作原理和受力机制,利用 自润滑推力轴承钢拉杆拉接、预应力钢束配合限位钢 梁连接、管周摩擦力等措施有效抵抗止水带回弹力,实 现管节接头张开量在5 mm以下的管节贯通连接,解决了常规陆域最终接头需另行设置大体量圬工结构, 经济性差的难题。
3)首次研发并量产了可满足0.3 MPa外水压水 密性、100年设计使用寿命的沉管接头外侧止水带国 产化产品,其百年应力松弛衰减率仅25.5%,预测使 用寿命144年;研制建立了生产工艺方法和自动化生 产线,打破了中国沉管接头GINA止水带被国外“卡脖子”垄断状况,首次实现了中国沉管隧道全产业链技术的国产化。
4)首次提出了整体式管节不设后浇带全断面顺 浇预制工法,研发了混凝土材料、温度控裂、浇筑工艺 和设施设备等成套关键技术和装备,实现了沉管结构 预制工效提高52%,结构接缝减少57%,浇筑裂缝减少60%,解决了常规工法存在的工期长、接缝多、防水效果差等问题。
5)首次研发了全浮式高精度先铺卵石基床整平 船,装备配置可旋转抛石管和自动移船控制系统,实现了单垄3 min内一键自动化移船,基床整平精度不低 于±3.5 cm。
6)首次研发应用了沉管无焊接装配式端封门和 柔性水袋压载水系统,实现了舾装设施的便捷循环使 用和施工效率提升。 在当前城市基础设施高质量建设要求的大背景 下,未来内河沉管隧道建设仍需进一步提升融合环保 建设理念,进一步研究钢板混凝土组合结构沉管、无干坞浮态浇筑等新技术的应用。
在当前城市基础设施高质量建设要求的大背景 下,未来内河沉管隧道建设仍需进一步提升融合环保 建设理念,进一步研究钢板混凝土组合结构沉管、无干 坞浮态浇筑等新技术的应用.鱼梁洲隧道从关键技术、核心装备、特殊材料、智能建造等多个领域入手,实现国内首条沉管隧道建设全产业链国产化,并诞生了“三个最大”:世界最大规模千米双轴线沉管预制干坞、国内最大规模临江超厚砂卵石强透水地层超深超大基坑、国内最大规模超深格型地连墙岸堤防护结构,以及“七个首创”:国内首次采用移动工厂法整体式沉管全断面顺序浇筑工艺、世界首次采用无焊接装配式端封门结构、国内首次采用国产GINA止水带、世界首次采用先铺卵石基础工艺、国内首次采用全漂浮式整平船进行水下基床铺设、世界首次采用柔性压载水袋进行管节压载、国内首条陆域最终接头不设止推构造的沉管隧道,对引领内河沉管隧道技术发展具有重要意义。
根据长江日报、隧道建设今日襄阳等综合整理