0 引言
全断面隧道掘进机具有施工速度快、效率高、隧道
成型好、对周边环境影响小、作业安全及节省劳动力等
优点,已广泛应用于铁路、水利水电、城市轨道工程以
及煤矿巷道工程等领域 。 但在采用隧道掘进机施
工过程中,因为机型选择不当或者参数不合理导致工
程效率低下、人为掘进控制不到位出现地表沉降甚至
塌陷、盲目运行维护造成刀具刀盘损坏等案例较多,这
些问题造成了巨大的经济损失和恶劣的社会影响。 由
于隧道掘进机装备结构复杂、施工环境恶劣,给全断面隧道掘进机制造、运行与维护带来了诸多的难题与挑战。
进入 21 世纪以来,人工智能、物联网和大数据的
发展掀起了产品智能化的巨浪。 新信息技术与产品的
融合发展,给装备制造业运维带来了新的契机。 基于
此,世界各国纷纷将装备智能化规划为国家战略发展
方向,其中包括“中国制造 2025”、 “ 中国人工智能
2. 0”、德国“工业 4. 0”、美国“国家制造创新网络计
划”、日本“新机器人战略计划”、英国“高价值制造战
略”以及韩国“新增长动力规划及发展战略”,促进了
装备智能制造的快速发展。 当前,国内外一些学者和
专家对全断面隧道掘进机智能制造和运维技术进行了
一些研究,全断面隧道掘进机施工基本实现了配套化
作业,建立了远程信息管理系统,实现了装备运行实时
监控。 但以隧道掘进机为中心的群组装备配套作业施
工互联技术较为落后、装备群组协同困难,制约了隧道
掘进机的运行效能。 另外,全断面隧道掘进机作为大
型隧道施工专用装备,运行维护直接影响工程施工、装
备设计制造,因此全断面隧道掘进机制造/ 运维在产品
全生命周期上呈典型跨域分布,导致严重信息孤岛,
制约了装备制造技术迭代与转型升级。 当前亟需采
用智能技术推动产品制造和运维转型升级,建立全
断面隧道掘进机数据跨域共融共享机制,形成装备
设计协同方法,研发智能感知采集终端,深度挖掘应
用数据,创新“以用户为中心” 的价值网服务商业模
式,推动全断面隧道掘进机制造、运维技术发展和产
业转型升级。
1 智能制造技术研究现状
智能制造是基于数字化、网络化制造技术,智能技
术,数据驱动与软件定义技术构建“态势感知—实时
分析—人机决策—优化执行—自主适应” 的数据闭
环,以软件控制数据的自动有序流动来消除复杂系统
的不确定性,在给定的时间、目标场景下,优化资源配
置的一种制造模式。 装备智能制造的发展经历了信息
化和工业化的深度融合过程。
全断面隧道掘进机作为典型的复杂高端隧道施工
专用装备,零部件众多、结构复杂,总体选型、协同设计
至关重要,众多工程运维反馈的协同制造体系亟待形
成。 目前,已有许多专家和学者对装备智能制造进行
了研究与应用,但总体处于起步阶段。 现有方法对装
备制造单一环节提供了参考或者个性解决方案,智能
制造的整个流程还不能形成有效的闭环,全断面隧道
掘进机智能制造技术研究刚刚起步。
何小新等开发了基于人工神经网络和范例推
理系统的功能模块,建立了全断面隧道掘进机智能选
型方案生成系统原型。 彭卫平等以全断面岩石隧
道掘进机后配套运输方案设计为例,结合规则推理和
虚拟现实技术,提出了人机智能协同工程装备方案设
计方法,建立了人机智能协同工程装备方案设计环境,
并结合工程实际,在该环境下实现了隧道掘进机后配
套运输系统方案选型、设备布局和虚拟仿真。 王增强
等基于复杂零件的工艺流程,建立以逻辑制造单元
为核心的网络化制造单元资源优化配置问题模型。 范
孝良等通过构建人工神经网络模型,获取了加工特
征的加工方法,但是没有与设备信息进行关联。 易树
平等 为了实现装备制造智能化环境下工艺规划决
策目标,优化制造资源配置,提出了面向智能车间的工
艺规划辅助决策方法,但鉴于智能车间产品加工的复
杂性,多品种复杂零件在智能环境下的工艺规划及资
源配置问题是下一步研究的重点。
2 智能运行技术的研究基础分析
在全断面隧道掘进机智能运行技术研究方面,截
至目前,已有很多研究和产品用于全断面隧道掘进机
的智能运行掘进过程,包括施工地质超前预报、掘进状
态感知、掘进参数与地质参数匹配、主动参数优化与被
动参数预警以及掘进状态智能控制与优化决策等方面 。 当前,国内外较多学者和研究机构针对全断面
隧道掘进机智能运行技术进行了数智化探索,主要侧
重于超前地质预报、掘进运行状态智能感知预测、掘进
运行数据挖掘与智能应用等方面,取得了较多成果,为
行业技术发展提供了较好基础。 但整体来看,成果基
本是关于传统全断面隧道掘进机 PLC 集成分布式控
制系统方面的,侧重算法与应用研究。
2. 1 超前地质预报
在超前地质预报方面,全断面隧道掘进机施工工
法与传统的钻爆法相比具有本质不同。 掘进机本身的
结构复杂性和对电磁场的强烈干扰性,决定了传统钻
爆法的超前地质预报很难适用于全断面隧道掘进机施
工环境。 多年来,研究者致力于进行全断面隧道掘进
机超前地质预报技术研究,取得了突破性的成果,实现
了全断面隧道掘进机系统的搭载应用,但成果应用偏
少,用于实际工程并指导工程实践的案例不多。
以 TBM 掘进破岩震动作为被动震源的地震反射
法首先被引入 TBM 环境的超前地质预报领域,开启了
全断面隧道掘进机超前地质预报的新思路。 Kneib
等将随钻地震探测技术引入 TBM 自动探测,提出了
隧道 随 钻 地 震 超 前 探 测 技 术 ( tunnel seismic while
drilling,TSWD),即将地震波传感器安装在 TBM 护盾
或隧道边墙上以测量地震反射信息,通过数字滤波等
技术压制被动震源中的干扰。 但是由于刀盘及刀具破
岩激发的声波信号频带较宽且频率复杂,频带密集、杂
乱,各种杂波干扰严重,有效波的识别与分离十分困 难。 卢松等[9] 针对被动震源超前地质预报方法存在
的问题,基于地震波干涉理论,通过分析多滚刀同步破
岩振动信号的干涉特性,揭示了 TBM 掘进刀盘多滚刀
同步破岩震源波场的传播规律,提出了波场反射信息
识别方法; 利用波场传播的反射与散射特性,建立了
TBM 掘进状态下反射波与散射波联合成像方程,开发
了岩体地震波阻抗差异参数的智能成像软件,最终发
明了 TBM 掘进状态下以滚刀破岩振动为震源的实时
超前地质预报方法(如图 1 所示),实现了 TBM 连续掘
进状态下的实时超前地质预报。
图 1 以滚刀破岩振动为震源的隧道超前地质预报方法
李术才等研发了以不同地质介质之间的激电
效应差异为物质基础的激发极化法超前地质预报方
法,并在国产自主研发的全断面隧道掘进机上搭载运
用,如图 2 所示。 德国 Geohydraulic data 公司将 BEAM
技术应用于全断面隧道掘进机施工的超前地质预报,
实现了探测仪器、传感器与掘进装备的集成运用。 但
由于该探测方法和理论的局限性,其在定位精度、探测
距离、分辨率等方面存在很大问题,难以满足隧道施工
需要。
图 2 TBM 搭载激发极化法超前地质预报系统
2. 2 掘进运行状态智能感知预测
在掘进状态感知方面,郑伟等研发了一种基于
电涡流传感器的滚刀刀圈磨损量在线监测系统,用以
在隧道掘进机破岩过程中实时监测盘型滚刀的磨损
量。 该方法通过室内试验验证可行,其具体监测原理
如图 3 所示。
图 3 基于电涡流传感器的滚刀刀圈磨损量在线监测原理
赵海雷等采用静电纺丝与气相还原氮化相结
合的方式制备了塞隆体系带状荧光纳米纤维膜,薄膜
微观上保持带状纤维结构,宏观上保持薄膜状态,高温
条件下表现出较低的荧光衰减结果和较高的机械强
度,理论上可将纤维膜和滚刀有机结合用于滚刀磨损
程度的实时监测,减少带压和高风险地质段的人工检
测。 荧光纤维膜制备机制如图 4 所示 。
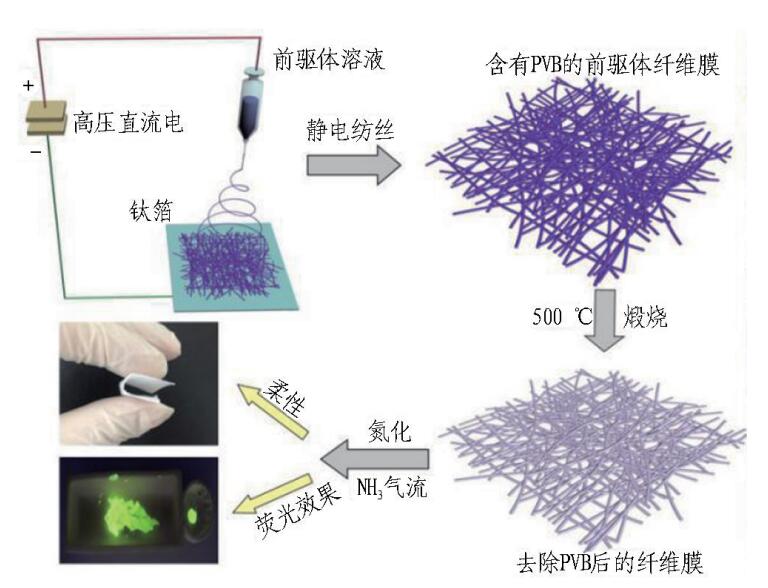
图 4 荧光纤维膜制备机制
张晓波等[13]对全断面隧道掘进机进行刀盘振动现场监测,并对振动响应进行时域及频域分析。 一些
学者建立了基于虚拟仪器的振动模态理论、振动监测
系统以及多参数磨损预测模型,为全断面隧道掘进机
掘进状态预测提供一些技术支撑。
通过监测分析刀盘、刀具传感器信号监测掘进机
运行性能的方法,存在的主要问题是缺少系统化的数
据感知理论和实时反馈调控方法,结构性数据已经基
本融合和互馈,但非结构性数据还没有实现动态化融
合与分析,不能做到岩机状态的动态评价识别。
2. 3 掘进运行数据挖掘与智能应用
在掘进参数与地质参数匹配研究方面,赵博剑
等进行了复合地层盾构掘进参数及其与地层的相
关性分析。 意大利 Geodata 公司建立了隧道工程施工
监测信息化管理 GDMS 系统,已在俄罗斯圣彼得堡、
意大利罗马和圣地亚哥等城市轨道交通建设中使用。
国内也开发了相应的盾构 TBM 大数据应用平台,例
如: 通过数据采集、智能监控,基于大数据技术和科学
的海量数据分析以及实时感知与快速反演的信息化技
术,搭建的智慧盾构 TBM 工程大数据平台,可用于盾
构掘进参数分析、风险预警与辅助巡航等。
在掘进状态智能控制与优化决策方面,国内外做
了大量的研究和实践。 在煤炭领域,一些学者综合应
用自动化、智能化和信息化等高新技术开发了适合煤
矿掘进工作面地质与环境条件的掘进机远程控制技术
及监控系统,实现了掘进机位姿参数在线自动检测、自
动定向掘进。 于睿坤在对盾构姿态人工控制过程
进行深入研究的基础上,结合现有盾构的实际情况,设
计了一套集姿态自动测量、地质勘查与探测、模糊智能
控制、远程在线监控于一体的盾构掘进姿态智能控制
系统,可以对盾构施工进行控制与辅助优化决策。 但
该项工作目前仅停留在理论研究阶段。 日本科学家
Okubo 等基于多个 TBM 预测模型与已建 TBM 隧道
数据,开发了一套适用于 TBM 隧道的决策系统。 盾构
及掘进技术国家重点实验室基于盾构工程大数据平
台,开发了智慧掘进辅助巡航与智能掘进自主运行系
统,如图 5 所示。 智慧掘进辅助巡航系统用于指导装
备运行,目前已用于行业 300 多个工程。 智能掘进自
主运行模式在辅助巡航的基础上融合边缘计算和终端
控制技术,实现了云边端架构的盾构本地操作/ 智能掘
进一键切换,该系统已用于上海机场联络线盾构隧道
工程,在黏土、粉细砂等软土地层已成功应用。
图 5 盾构智慧掘进辅助巡航与智能掘进自主运行系统
总体来看,目前国内外地质参数与掘进参数匹配
的智能化掘进管理平台功能还不够完善,主要停留在
施工监测与数据收集阶段、信息化应用阶段,对于智能
研究进行了一些数据挖掘工作,研发了智能掘进系统,
但这些数据挖掘多限于单个工程或者单一地层。 另
外,基于大数据支撑的云边端辅助巡航智能掘进系统
控制架构重新设计和数据深度挖掘还需继续研究。
3 智能诊断与维护技术研究进程
在全断面隧道掘进机智能运维和健康管理方面,
国内外学者虽然做了大量的研究,但成果主要侧重于
理论研究、智能推理或者信息化统计分析、预警应用方
面,基于大数据的装备健康评估、故障诊断、资源调配
等智能维护技术体系还没有完全形成。 随着科技的进步,发展制造资源指导、大数据驱动的运行停机多阶段
状况评估、实时的故障诊断与资源调配技术、融合新一
代信息技术的智能运维系统,将是全断面隧道掘进装
备智能运维健康管理的研究重点。
目前,航空航天、基础建设和工业应用等各个领域
的工程系统日趋复杂,系统的综合化、智能化程度不断
提高,产品研制、生产尤其是维护和保障的成本越来越
高。 同时,由于组成环节和影响因素的增加,发生故障
和功能失效的概率逐渐增大。 因此,高端装备的智能
运维和健康管理逐渐成为研究者关注的重点。 目前,
国内关于全断面隧道掘进机智能运维和健康管理的研
究还处于初始阶段。
在国内,一些学者进行了盾构关键设备状态监测
与故障诊断研究与分析。 张东雪充分利用海量的
TBM 故障数据,利用建立的故障诊断基本模型(如图 6
所示),开展了基于数据挖掘技术的全断面隧道掘进
机故障诊断系统研究,将故障案例库中海量状态数据
与对应发生的故障之间潜在的规则挖掘出来,以便能
快速准确地定位故障。 李凤远等针对盾构振动信
号的故障特征频率不易提取的问题,提出一种基于
LCD(局部特征尺度分解)和 FastICA(快速独立分量分
析)相结合的故障诊断方式,相比于固有时间尺度分
解,该方法能够减少外界噪声的干扰,更好地提取出机
械振动信号的故障特征频率。 在国外, Marcelo G.
Simoes 和 Taehong Kim 利用模糊逻辑理论研究了一套
TBM 使用性能预测系统;德国 Wirth 公司对 TBM 的主
轴承、齿轮箱的润滑油以及液压油的油位、油温、油滤
芯堵塞、电气系统参数等配置了在线监测装置,所有监
测数据均被记录,并为 PC ( 计算机) 控制中心提供
报告。
图 6 故障诊断的基本模型
4 智能安装与机器人技术的探索与应用
在隧道复杂结构同步智能安装与机器人技术的研发应用方面,国内外一些研发团队进行了研究和工程应用,推动了隧道智能建造水平,促进了全断面隧道掘进机智能化水平。
熊志林开展了盾构刀具检测蛇形臂机器人(如
图 7 所示)关键技术研究,设计了中空的蛇形臂、关节
及驱动模块,建立了机器人空间规划坐标与控制架构
等。 中铁隧道局集团有限公司开展了大直径盾构隧道
底部弧形件同步智能拼装机(如图 8 所示)的研发,安
装精度提高到 mm 级以内,作业效率较人工拼装提高
了 6 倍,目前已成功应用于上海机场联络线工程。
图 7 盾构刀具检测蛇形臂机器人
图 8 弧形件同步智能拼装机
在隧道结构盾构装备智能安装方面,日本日立公
司以伺服控制为基础,采用光学图像、激光与传感检测
技术,构建管片特征检测与感知、空间动态检测方法和
复杂系统的运动控制方法,研制了 6 自由度管片自动
安装机器人,用于管片拼装的全自动化。 法国布依格
( Bouygues Construction ) 团 队 研 发 了 Dobydo &
Krokodyl 机械臂和 Atlas 管片拼装机器人,如图 9 所
示。 Dobydo & Krokodyl 机械臂主要是基于 AI 视觉的
盾构隧道管片间支撑木块的移除,Atlas 管片拼装机器
人主要是基于机器人技术的盾构隧道管片抓取作业。
德国海瑞克公司基于水枪、灯光、相机与内窥镜等技术
研发了可延展机器人。
图 9 Dobydo & Krokodyl 机械臂和 Atlas 管片拼装机器人
5 发展趋势
总体来看,当前全断面隧道掘进机智能制造研究
刚刚起步,基于装备传统控制的智能运行技术正在蓬
勃发展,有效的智能诊断维护技术体系还未形成,智能
安装与机器人技术已经开始了探索与应用。 随着新一
代信息技术高度发展,各行各业大数据与实体经济深
度融合,全断面隧道掘进机智能制造/ 运维发展将呈现效用驱动的机制深度融合、核心技术集中攻关、智能整体集成综合态势,逐步形成制造/ 运维互馈集成价值网平台,推动产业转型升级。
5. 1 亟待形成基础数据融合集成机制
当前我国装备制造业不再是解决“有没有” 的问
题,而是重点解决“好不好”的问题,全断面隧道掘进
机属于典型的个性化、多样化、小批量高端装备,也是
我国装备制造业现阶段发展的重大需求,效能驱动不
再是简单机器换人、自动化、无人工厂能够实现的,系
统的、多维度的、全价值链的数据与应用集成已是迫切
需要的。
全断面隧道掘进机制造和运维的成套装备运行交
互感知水平低、协同制造业与运维基建施工业互馈机
制缺失,传统的协调方式已经不能满足装备快速发展
的需要,随着计算机、物联网、大数据的发展,制造/ 运
维协同预测将成为重要解决方式。 打破全断面隧道掘
进机制造/ 运维跨越数据壁垒,需要形成核心企业主导
全断面隧道掘进机制造和运维应用数据融合集成共享
体制机制,重点开展多场点多主体异构数据融合方法、
分布式协同的安全多方计算技术、分布式数据池融合
数据湖集成技术等研究,实现面向装备制造和运维协
同的实时、高效、共享的数据支持,夯实全断面隧道掘
进机制造和运维智能化发展的基础。
5. 2 亟待研发多元异构数据采集智能终端
当前传感器技术飞速发展,全断面隧道掘进机基
本实现了智能互联互通。 但是作为地下交通的重要建
造装备,面临的地质环境复杂多变,感知机制与技术依
然不成熟,“人-机-环” 智能交互依然停留在探索阶
段;以全断面隧道掘进机为中心的成套装备优化运维
赛博物理系统,需要实现多体异构数据的交互感知;另
外,全断面隧道掘进机群组制造是一个分布式集群社
会化大协同的过程,各部件制造数据的协同交互也将
是数据集成的重要内容。
多元异构数据交互感知设备与采集技术亟待突
破,针对全断面隧道掘进机制造和运维数据多源性、异
构性和分布性特点,应研究多源异构数据自适应采集
方法、研发匹配异构装备多接口共融程序;针对多群组
多主体装备组网灵活多变且经常调整的问题,研制基
于 5G 技术的智能采集和反馈终端;针对传统采集中
存储无法满足海量大数据的需要,研究面向智能互联
装备制造和运维数据分布式存储于接口技术,建立数
据共融、自适应交互、高效、共享、实时、灵活的语义数
据环境。
5. 3 亟待突破装备群组分层制造协同技术
网络协同制造技术是一种先进的制造方式,充分
利用以 Internet 技术为特征的网络技术、信息技术,将
串行工作变为并行工程,实现供应链内及跨供应链间
的企业产品设计、制造、管理和商务等合作。
基于国际竞争力的提升需要,全断面隧道掘进机
作为典型的复杂高端装备,零部件众多,系统集成社会
化大生产是高效制造的关键,整机及核心部件亟需集
成现有单环节闭环智能制造技术,突破以主机厂为中
心基于联邦模式的分层协同制造的整体集成技术。 基
于联邦模式的分层协同技术,既可实现系统之间的资
源共享与协同工作,又维持了各系统的自治性,使得任
何系统的加入和退出都不影响其他系统的运行[20]
。
在智能互联成套装备群组数据采集及融合技术上,分
析掘进机群组协同设计制造的关键构成要素,构建运
维知识驱动的装备设计制造多要素协同机制模型;将
大数据技术与机制模型融合,创新运维数据驱动的全
断面隧道掘进机协同优化选型设计理论,形成精准选
型方案;研究成套装备的制造资源建模技术,综合考虑
物流运输与生产服务能力等因素,构建成套装备群组
协同制造的动态分布式生产调度模型,形成设计/ 生产
多层次符合协同技术,实现产品制造性能和生产效率
的提升。
5. 4 机制-数据混合驱动的云边端分布式智能运维系统是重要研究方向
全断面隧道掘进机集机、电、液、信息技术于一体,
系统庞大、结构复杂。 设备结构的复杂性和功能的耦
合性决定了微小的故障可能引起连锁反应,导致设备
无法安全可靠地运行、及时地维护和备件调度。 传统
大型复杂装备基于运行机制和控制机制的大中型 PLC
集成本地分布式控制技术,具有本地连锁控制特点,但
是已经不能适应未来大型复杂装备云端预测大数据支
撑、边缘计算双向反馈与终端控制应急熔断的智能运
行与维护的需要。
未来的隧道掘进机智能运行,将不再是简单的
“云+传统 PLC”集成控制模式,需要重构现有全断面
隧道掘进机控制系统,“以工程建造需求” 为中心,构
建工程大数据支撑的“云-边-端”分布式控制架构,实
现大数据云端预测引领多工程全局预测;部署项目边
缘服务器单工程集成控制,实现项目工程多方智能汇
聚;嵌入式智能终端和集成式 PLC 控制相融合,传统
PLC 集成控制将升级为边缘服务器集成分系统、分功
能多方智能终端的分布式控制新模式;机制-数据混
合驱动的云边端分布式智能运维系统是重要研究
方向。
5. 5 “以用户为中心”的制造/ 运维价值网服务平台是产业转型的未来趋势
互联网、云技术、大数据的发展,推动装备从制造
向服务化转型,要创造以用户为中心的新的经营模式,
以更高效率把产品传递给用户,给用户带来新的价值,
“制造+服务”的发展模式已成为装备制造业与生产服
务业发展的方向。 全断面隧道掘进机产业作为我国新
型战略产业中的高端装备制造业,产品设计生产应用
服务产业链条长,将带动社会上下游企业发展。
通过探索 TBM 制造业服务化实现路径和服务化
模式,研究制造企业主导的制造服务价值网融合理论
方法与数据驱动的装备服务关键技术,先进制造企业
应充分利用模块化和价值网络带来的便利条件,不断
提高产品的规模实力,提升企业的技术创新水平。 探
索以“用户为中心”的全断面隧道掘进机设计、采购、
制造、销售和服务等产品全生命周期的价值网融合协
同模式,突破制造/ 运维互馈技术,研发制造/ 运维集成
服务云平台,实现协同设计制造、运行保内保外服务、
故障预警、计划维修、配件管理等流程再造,促进产品
制造向产品服务的延伸,提升产品质量、优化产品运
行,改变传统 TBM 装备制造及运行的模式。
6 结论与展望
计算机、互联网、物联网、虚拟制造、网络协同制
造、云计算与大数据的发展,快速推动了全断面隧道掘
进机智能化的进程。 总体来看,隧道掘进机智能制造
刚刚起步,国内外学者基于传统装备控制系统进行了
智能运行研究,在个别系统或者部分领域进行了装备
智能运维探究,在行业进行了智能机器人技术探索研
究与应用。 当前,高性能计算机得到了快速发展,为全
断面隧道掘进机工程大数据平台的搭建提供了基础;
5G 等物联网关键技术包括射频识别技术、网络通信技
术、传感器技术和云计算技术等成熟发展,推动了全断
面隧道掘进机成套装备群组智能互联;CAD、BIM 等工
程技术量化发展,使隧道工程趋向固定的算法发展,为
全断面隧道掘进机制造/ 运维智能决策提供了必要条
件。 基于全断面隧道掘进机研究现状,建立多方数据
融合机制,突破多源异构数据采集、分层制造生产协同
等关键技术,研发机制-数据混合驱动的云边端分布
式智能运维系统,对于装备制造/ 运维具有重要现实意
义,跨域构建“以用户为中心” 的制造/ 运维价值网服
务平台,将推动全断面隧道掘进机制造/ 运维产业转型
升级。